PDCA Cycle atau Siklus PDCA adalah suatu metode pemecahan masalah dalam pengendalian kualitas, melalui siklus empat langkah : Plan, Do, Check, Action.
Pengertian PDCA Cycle
PDCA adalah akronim dari “Plan, Do, Check, Action” yang digunakan dalam bisnis untuk pengendalian dan perbaikan berkesinambungan (continuous improvement) bagi proses dan produk.
Konsep PDCA merupakan pedoman bagi perusahaan untuk proses perbaikan kualitas secara terus menerus tanpa berhenti.
Jadi menuju peningkatan ke arah keadaan yang lebih baik dan dijalankan di seluruh bagian organisasi.
Struktur PDCA Cycle
Berikut ini adalah penjelasan dari struktur siklus PDCA atau PDCA Cycle.
P = Plan : Rencana, mengidentifikasi dan menganalisis masalah
Tetapkan tujuan dan proses yang diperlukan untuk memberikan hasil yang diinginkan atau sesuai dengan standar maupun spesifikasi.
Pada tahap ini kita dapat menggunakan beberapa alat bantu kualitas (quality tools) untuk membantu menemukan akar masalah, seperti :
- Drill Down
- Cause and Effect Diagram
- 5 Whys
Setelah berhasil mengidentifikasi, maka kita dapat memetakan proses tersebut.
Selanjutnya adalah menggambarkan semua informasi lain yang diperlukan untuk membantu dalam menemukan solusi.
D = Do : Kerjakan, mengembangkan dan menguji solusi yang terbaik
Laksanakan tujuan dari langkah sebelumnya yakni penerapan atau implementasi di proses, mengembangkan dan menguji solusi yang berpotensi
Pada fase ini ada beberapa langkah diantaranya adalah :
- Mengusulkan solusi yang memungkinkan.
- Memilih solusi terbaik, dapat digunakan metode Impact Analysis.
- Melakukan implementasi solusi sementara pada contoh kasus skala kecil terlebih dahulu (trial).
Pada tahap ini, tindakan yang dilakukan belum dapat diterapkan secara secara penuh, penerapan maksimal akan dilakukan pada tahap Act.
C = Check : periksa
Memantau dan melakukan evaluasi terhadap proses dan hasil dibandingkan dengan sasaran dan spesifikasinya, kemudian melaporkan hasilnya.
Selama tahap pemeriksaan, data dan hasil dikumpulkan dari tahap evaluasi.
Data dibandingkan dengan hasil yang diharapkan untuk melihat apa saja persamaan dan perbedaannya.
Proses pengujian juga dievaluasi untuk melihat apakah ada perubahan dari pengujian yang dilakukan selama tahap perencanaan.
Jika data ditampilkan dalam bentuk grafik maka akan lebih mudah untuk melihat tren jika siklus PDCA tersebut dilakukan beberapa kali.
Hal ini dapat membantu untuk melihat perubahan apa saja yang hasilnya lebih baik dibanding lainnya, serta memutuskan apakah perubahan tersebut juga dapat ditingkatkan.
Contoh: Gap analysis, appraisal.
Pada fasa ini diukur seberapa efektif solusi sementara yang telah dibuat.
A = Action : Tindak lanjut
Menindaklanjuti hasil untuk membuat perbaikan yang diperlukan.
Hal ini berarti juga meninjau seluruh langkah dan memodifikasi proses untuk memperbaikinya sebelum implementasi berikutnya.
Hasil dari identifikasi masalah proses dari fase Do dan Action, kemudian diperbaiki di Fase siklus ini.
Contoh permasalahan yang diidentifikasi :
- Ketidaksesuaian
- Peluang untuk adanya perbaikan
- Ketidakefisienan
- Masalah lain yang menyebabkan hasil yang kurang optimal.
Setelah identifikasi maka akar penyebab masalah tersebut diselidiki, ditemukan dan dihilangkan dengan melakukan modifikasi proses.
Selanjutnya risiko tersebut dilakukan evaluasi ulang, maka saat akhir tindakan dalam fase ini, proses tersebut dapat memiliki suatu instruksi, standar atau tujuan yang lebih baik.
Sebagai catatan, seharusnya masalah yang sama tidak ditemukan lagi setelah dilakukan perbaikan, jika masih ada maka artinya bahwa tindakan perbaikan yang sudah dilakukan tidak efektif.
Siklus PDCA atau PDCA Cycle
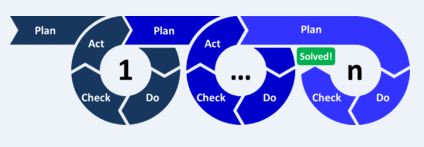
Penerapan siklus PDCA ini bisa dilakukan berulang-ulang hingga masalah terpecahkan, karena prinsip fundamental dari metode ilmiah dan PDCA adalah iterasi.
Jadi setelah hipotesis atau rencana dari fase Plan sudah dikonfirmasi pada fase Act, maka siklus dapat diulang lagi lagi.
Pengulangan suatu siklus PDCA dapat menyempurnakan hasil yang diperoleh dari satu kali siklus PDCA yang dilakukan.
PDCA atau bentuk pemecahan masalah ilmiah lainnya juga dikenal sebagai sistem untuk mengembangkan pemikiran kritis.
Di Toyota, hal ini juga dikenal sebagai “Membangun orang sebelum membuat mobil”.
Toyota dan perusahaan Lean Manufacturing lainnya menyatakan bahwa tenaga kerja yang terlibat dengan PDCA akan lebih mampu melakukan inovasi dan mampu bersaing dalam pemecahan masalah.
Deming terus menekankan iterasi untuk menuju sistem yang lebih baik, oleh karena itu PDCA harus diterapkan secara berulang kali.
Rangkaian dari siklus tersebut akan semakin meningkatkan pengetahuan tentang sistem, setiap cycle bertambah maka akan semakin mendekati tujuan pencapaian akhir.
Analoginya adalah sebuah pegas atau peer yang terbuka, setiap putaran atau cycle menandakan peningkatan pengetahuan tentang sistem yang dipelajari.
Pendekatan ini berbasis suatu keyakinan bahwa pengetahuan dan kemampuan itu terbatas, namun dapat terus ditingkatkan.
Tujuan dari siklus PDCA adalah untuk membantu penggunanya mencapai lebih dekat ke tujuan setiap kali siklus dijalankan.
Ketika PDCA diterapkan untuk menjalankan proyek atau produk yang kompleks dengan permasalahan lhusus, pemeriksaan dengan pemangku kepentingan eksternal harus dilakukan sebelum tahap Do.
Hal ini karena perubahan pada proyek dan produk yang sudah dalam dase desain lebih lanjut bisa jadi membutuhkan biaya yang lebih mahal.
Kapan waktu yang tepat untuk penerapan PDCA Cycle?
Berikut beberapa waktu terbaik yang dimaksud :
- Saat mengimplementasikan Kaizen atau perbaikan berkelanjutan (continuous improvement)
- Ketika mengidentifikasi solusi dan improvement baru untuk sebuah proses yang dilakukan secara berulang-ulang.
- Dalam mengeksplorasi range dari solusi baru yang memungkinkan untuk memecahkan masalah dan menguji sekaligus meningkatkan solusi tersebut dengan implementasi kontrol yang lebih baik.
- Menghindari pemborosan sumber daya dalam jumlah besar yang dapat terjadi jika implementasi dilakukan tanpa pengujian terlebih dahulu.
Jelas sekali menggunakan PDCA adalah suatu pendekatan yang lebih lambat daripada melakukan implementasi straightforward dari gung ho.
Dalam keadaan mendesak tentunya tidak perlu lagi melakukan tindakan ini.
Namun, perusahaan akan mendapat keuntungan yang lebih besar jika menerapkan PDCA pada timing atau waktu yang tepat.
Sejarah PDCA Cycle
Metode PDCA ini dipopulerkan oleh W. Edwards Deming, sang bapak pengendalian kualitas modern, sehingga metode ini juga sering disebut dengan siklus Deming.
Deming menganggap metode ini adalah pengembangan dari siklus Shewhart, yang ditemukan oleh nama Walter A. Shewhart, sang penemu SPC (Statistic Process Contol).
Namun menurut Deming, metode PDSA (Plan, Do, Study, Action) lebih tepat dibandingkan metode PDCA.
Karena dia merasa bahwa istilah “check” menekankan pemeriksaan, sedangkan istilah “Study” lebih menekankan pada analisa.
Versi lain dari PDCA adalah OPDCA, dengan tambahan karakter “O” yang berarti observation atau lakukan observasi untuk kondisi saat ini.
Penekanan pada observasi dan kondisi saat ini berdasarkan literatur dari konsep Lean Manufacturing dan TPS (Toyota Production System).
Konsep PDCA didasarkan pada metode ilmiah, yang dikembangkan dari karya Francis Bacon (Novum Organum, 1620).
Metode ilmiah dapat ditulis sebagai ” hypothesis–experiment–evaluation” atau sebagai ” plan–do–check”.
Walter A. Shewhart mendeskripsikan proses produksi manufaktur yang terkendali (terkendali statistik), sebagai proses tiga langkah :
- Spesifikasi
- Produksi
- Inspeksi
Dia juga secara spesifik mengaitkan hal ini dengan metode ilmiah :
- Hipotesis
- Eksperimen
- Evaluasi
Shewhart mengatakan bahwa ahli statistik “harus membantu proses produksi dengan cara mengurangi variasi dan meningkatkan kualitas produk.
Jadi Shewhart bermaksud melakukan analisa untuk mengambil tindakan berdasarkan kesimpulan hasil evaluasi.
Menurut Deming, selama perkuliahannya di Jepang pada awal 1950-an, peserta kuliah mempersingkat langkah-langkahnya menjadi konsep : plan, do, check, act.
Namun Deming lebih memilih plan, do, study, act, karena kata “study” memiliki konotasi dalam bahasa Inggris yang lebih mendekati keinginan Shewhart daripada kata “check”.
Perbedaan Standar Metode PDCA vs DMAIC
Pada penerapan di berbagai perusahaan, umumnya teknik PDCA digunakan dalam kegiatan Kaizen.
Sedangkan metode lain yang sejenis yaitu DMAIC (Define, Measure, Improve, Control) dipergunakan pada aktivitas Lean Six Sigma.
PDCA sangatlah cocok untuk dipergunakan untuk kegiatan perbaikan berkesinambungan (continuous improvement) skala kecil, seperti :
- Memperpendek siklus kerja
- Mengurangi atau menghilangkan pemborosan di tempat kerja.
- Meningkatkan produktivitas.
Sementara metode DMAIC lebih sesuai untuk skala besar seperti :
- Menghilangkan varian output
- Mengendalikan kestabilan mutu atau kualitas
- Perbaikan pada yield
- Penghematan biaya
- Efektivitas organisasi bisnis
Manfaat PDCA
Beberapa Manfaat dari PDCA antara lain:
- Untuk memudahkan dalam membuat peta wewenang dan tanggung jawab dari sebuah unit organisasi.
- Sebagai pola kerja dalam perbaikan suatu proses atau sistem di sebuah organisasi.
- Untuk menyelesaikan serta mengendalikan suatu permasalahan dengan pola yang runtun dan sistematis.
- Untuk kegiatan perbaikan berkesinambungan (continuous improvement) dalam rangka memperpendek alur kerja.
- Menghapuskan pemborosan di tempat kerja dan meningkatkan produktivitas.
Demikian artikel dari standarku.com mengenai Standar Metode Siklus PDCA.
Mohon saran dari pembaca untuk kelengkapan isi artikel ini.
Silahkan saran tersebut dapat disampaikan melalui kolom komentar.
Baca artikel lain :
- Standar Metode SPC Statistical Process Control
- Standar Metode Kualitas dari Edward Deming
- TQM Standar Metode Total Quality Management
Sumber referensi :